Extensive Butyl Acrylate Manufacturing Plant Project Report
In today’s competitive industrial landscape, the demand for Butyl Acrylate continues to rise, driven by its wide array of applications in the production of coatings, adhesives, plastics, and textiles.

In today’s competitive industrial landscape, the demand for Butyl Acrylate continues to rise, driven by its wide array of applications in the production of coatings, adhesives, plastics, and textiles. This chemical is produced by esterifying acrylic acid with butanol, a process requiring specific manufacturing techniques, efficient cost management, and careful consideration of feedstocks and market dynamics.
Request Your Free Sample Report - https://www.procurementresource.com/reports/butyl-acrylate-manufacturing-plant-project-report/request-sample
For businesses and investors aiming to tap into the potential of Butyl Acrylate production, a Butyl Acrylate Manufacturing Plant Project Report offers essential insights. This report delves deep into the core components of establishing a manufacturing facility for Butyl Acrylate, outlining critical factors such as the cost model, top manufacturers, feedstocks, market drivers, and manufacturing process. Moreover, the report provides a detailed look into the return on investment (ROI), ensuring that stakeholders make informed, profitable decisions.
1. Cost Model for Butyl Acrylate Manufacturing Plant
The cost model for a Butyl Acrylate manufacturing plant involves understanding various expense categories such as raw material costs, labor, energy, capital investment, and operational expenses. By considering these cost components, manufacturers can plan their budgets efficiently and optimize the production process.
The capital investment required for establishing a manufacturing unit for Butyl Acrylate depends on several factors, including plant capacity, location, and technology. Additionally, the ongoing operational costs—including utilities, maintenance, and wages—play a crucial role in determining the plant’s profitability.
To calculate the total cost of production, the report breaks down the cost per unit of production, factoring in raw material prices, labor, and overheads. Accurate cost predictions enable businesses to adjust pricing strategies, thereby improving their profit margins and competitiveness in the market.
2. Top Manufacturers in the Butyl Acrylate Market
The Butyl Acrylate market is led by several key manufacturers who have established a strong presence due to their advanced technology, extensive product portfolios, and economies of scale. These top players often enjoy significant market shares, thanks to their ability to deliver large volumes of high-quality product consistently.
Some of the leading manufacturers in the global Butyl Acrylate market include:
- BASF
- LG Chem
- ExxonMobil
- SABIC
- Mitsubishi Chemical
These companies dominate due to their vast infrastructure and extensive R&D investments. They continually innovate their processes to reduce production costs, improve product quality, and meet stringent regulatory standards. Understanding the competitive landscape in the Butyl Acrylate manufacturing sector is crucial for any potential new entrants.
3. Outline of the Manufacturing Process
The manufacturing process of Butyl Acrylate is relatively straightforward but requires precision in both chemical reactions and plant management. The most common method used is the esterification reaction, where acrylic acid reacts with butanol in the presence of a catalyst. This process typically occurs in a batch reactor under specific temperature and pressure conditions to ensure high yield and quality.
Read Full Report With Table Of Contents: https://www.procurementresource.com/reports/butyl-acrylate-manufacturing-plant-project-report/toc
The key stages of the manufacturing process are as follows:
- Preparation of Feedstocks: The raw materials, acrylic acid and butanol, are carefully measured and prepared. Butanol is a critical feedstock that influences the efficiency and cost of production.
- Esterification Reaction: The feedstocks are mixed in a reactor with the appropriate catalyst to facilitate the esterification process, converting acrylic acid into Butyl Acrylate.
- Purification and Separation: After the reaction, the mixture is cooled and separated, often through distillation, to purify the Butyl Acrylate.
- Packaging and Storage: The final product is then packaged and stored for distribution. The Butyl Acrylate can be stored in bulk or in smaller containers, depending on market demand.
Each stage of the process requires careful control of temperature, pressure, and reaction time to optimize yield and minimize waste.
4. Feedstocks for Butyl Acrylate Manufacturing
The primary feedstocks for Butyl Acrylate production are acrylic acid and butanol, which constitute the bulk of raw material costs. These chemicals are sourced from various global suppliers, with the prices of these commodities fluctuating based on supply-demand dynamics, geopolitical factors, and regional production capabilities.
The production of butanol, a key feedstock, can be derived from several processes, including the oxidation of butenes and fermentation of sugars. It is crucial for manufacturers to secure stable and cost-effective sources of butanol to ensure consistent production.
A key insight from the Butyl Acrylate Manufacturing Plant Project Report is the importance of securing long-term contracts with reliable feedstock suppliers. By doing so, manufacturers can minimize raw material price volatility and avoid production disruptions.
5. Market Drivers of Butyl Acrylate
The demand for Butyl Acrylate is driven by various factors, which include:
- Growth in the Coatings Industry: Butyl Acrylate is widely used in the production of paints and coatings due to its ability to enhance flexibility, durability, and weather resistance.
- Increasing Demand for Adhesives and Sealants: The use of Butyl Acrylate in adhesives, particularly for construction and automotive applications, continues to rise.
- Textiles and Plastics Applications: The increasing demand for high-performance textiles and plastic products also contributes to the growth of Butyl Acrylate production.
- Regulatory Support for Green Technologies: With increased demand for eco-friendly products, industries are turning to Butyl Acrylate as a safer alternative to other chemicals.
Understanding these market drivers helps businesses predict trends in demand and plan their production accordingly.
6. Key Insights on Investment and Return on Investment (ROI)
Investing in a Butyl Acrylate manufacturing plant can provide attractive returns, but careful planning is essential to maximize profitability. The return on investment (ROI) for Butyl Acrylate manufacturing depends on several key factors:
- Plant Capacity: The larger the plant capacity, the higher the initial capital investment. However, economies of scale can result in lower unit costs, improving profitability over time.
- Technological Advancements: Integrating the latest technologies can reduce energy consumption and increase production efficiency, leading to higher profit margins.
- Market Demand: The profitability of a Butyl Acrylate plant is closely tied to demand fluctuations in the end-use sectors. Continuous market analysis can help manufacturers adjust their production volumes to meet demand and secure higher prices.
- Regulatory Compliance: Compliance with environmental regulations and safety standards can incur costs, but non-compliance can lead to fines and operational shutdowns, negatively impacting ROI.
The Procurement Resource provides a comprehensive view of these factors, offering guidance on cost-effective solutions, risk management strategies, and opportunities for long-term profit maximization.
The Butyl Acrylate Manufacturing Plant Project Report offers a detailed analysis of the various components involved in establishing a profitable manufacturing facility for Butyl Acrylate. It covers crucial areas such as the cost model, feedstocks, market drivers, and the manufacturing process. Investors and manufacturers can use the insights provided to plan, execute, and optimize their operations.
By focusing on efficient feedstock procurement, process optimization, and technological advancements, businesses can ensure that their investment in Butyl Acrylate production delivers strong returns. For those looking to venture into the Butyl Acrylate market, understanding the report’s key findings can lead to more informed decisions and sustainable business growth.
For more detailed insights and real-time cost data, visit Procurement Resource and request further resources tailored to your specific needs.
Contact Us:
Company Name: Procurement Resource
Contact Person: Endru Smith
Email: sales@procurementresource.com
Toll-Free Number: USA & Canada - Phone no: +1 307 363 1045 | UK - Phone no: +44 7537171117 | Asia-Pacific (APAC) - Phone no: +91 1203185500
Address: 30 North Gould Street, Sheridan, WY 82801, USA
What's Your Reaction?
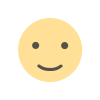
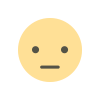
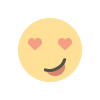
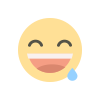
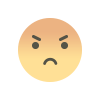
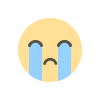
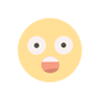