How Sheet Metal Fabricators Transform Your Designs into Reality
Discover how sheet metal fabricators turn your designs into reality with precision and advanced techniques like laser cutting and custom metal fabrication.

When it comes to bringing your designs to life, there is no better partner than a skilled sheet metal fabricator. Whether you are working on an architectural project, industrial machinery, or custom-made products, sheet metal fabricators can turn your ideas into solid, reliable products. Their expertise and tools, including laser cutting metal services and custom metal fabrication, are critical in shaping raw materials into intricate, functional designs.
What Is Sheet Metal Fabrication?
Sheet metal fabrication refers to the process of shaping metal sheets into specific products or parts. It involves a variety of techniques, including cutting, bending, welding, and assembling. The materials commonly used in metal fabrication include steel, aluminum, brass, and copper, though many other metals can be used depending on the project requirements.
It’s used in everything from building construction to automotive design, electronics, and even medical equipment. A professional sheet metal company will have the necessary tools and knowledge to execute the job accurately, ensuring that each piece meets the required specifications.
The Role of Sheet Metal Fabricators in the Design Process
Sheet Metal Fabricators are responsible for transforming raw metal sheets into the exact parts you need. Whether it's an intricate part for machinery or a custom architectural piece, the process starts with a design. Here’s a breakdown of the key steps involved:
Design and Planning
The process begins with a design. This can be a detailed blueprint or CAD (Computer-Aided Design) model that outlines the exact specifications of the part or product. The fabricator studies this design and develops a plan for how the metal will be shaped, cut, and assembled.
Material Selection
The next step is choosing the right type of sheet metal. Factors such as strength, flexibility, and resistance to elements like rust will dictate the choice of material.
Cutting and Shaping
The next step involves cutting and shaping the metal to match the design specifications. Advanced techniques, such as Laser Cutting Metal Services provide precise cuts with minimal waste. This ensures that the parts are accurate and of high quality. Laser cutting is one of the most advanced methods used by sheet metal companies today, allowing for intricate designs with sharp edges and smooth finishes.
Bending and Forming
After cutting, the next step is to bend or form the metal into the desired shape. Fabricators use various tools such as press brakes and rollers to bend the metal precisely according to the design. This process is essential when the design requires curves or specific angles.
Assembly and Welding
After the individual parts are cut, bent, and shaped, they are assembled together. In some cases, parts will be welded together to form a single unit. Welding creates a strong bond between the metal pieces, ensuring that the final product is durable and robust.
Finishing and Coating
Once the assembly is complete, the final step involves adding finishing touches. This can include coating the metal to prevent rust, painting it for aesthetic appeal, or polishing it for a sleek, smooth surface. These final steps ensure the product looks good and performs well under various conditions.
Key Techniques in Sheet Metal Fabrication
The field of Sheet Metal Fabrication involves numerous techniques, and each one has its own advantages depending on the type of project. Let’s look at some of the most common methods used by fabricators:
Laser Cutting
Laser cutting is one of the most precise and efficient methods for cutting sheet metal. A focused laser beam is directed at the metal, melting and vaporizing it to create a clean, accurate cut. This method is ideal for complex shapes and high-tolerance parts. Laser cutting also results in minimal material wastage, making it an environmentally friendly choice.
Bending and Rolling
Bending and rolling are common methods used to shape metal into specific angles or curves. Press brakes, rollers, and other specialized machinery are used to apply force and shape the metal to the desired curvature or angle. This process is widely used in industries that require cylindrical shapes, such as HVAC ducts or metal enclosures.
Punching
Punching involves using a tool to create holes or other shapes in a sheet of metal. This is often used in manufacturing parts that require perforations, such as grilles, panels, or vents. It’s a quick and effective way to create consistent and accurate holes in large quantities of metal sheets.
Welding
Welding is the process of joining two or more pieces of metal together using heat and pressure. It's essential for creating durable and high-strength parts, particularly in industrial and architectural applications. There are several types of welding techniques, including TIG, MIG, and stick welding, each suited to different types of metal and welding conditions.
Why Choose Custom Metal Fabrication?
One of the most appealing aspects of sheet metal fabrication is its versatility. Custom metal fabrication allows businesses to design and produce parts tailored specifically to their needs. Whether it’s a one-off project or large-scale production, custom fabrication ensures that you get exactly what you want, with no compromises.
For businesses, working with a sheet metal contractor that offers custom metal fabrication services can result in better, more efficient designs. It also opens up the possibility for innovation, as custom solutions allow for greater creativity in design.
Finding Sheet Metal Fabrication Near Me
If you are in need of a sheet metal fabrication near me, there are several options available. Many local fabricators offer a wide range of services, from custom designs to high-volume production. Whether you’re a small business or a large corporation, you can find a fabricator that can meet your specific needs.
By choosing a local sheet metal company, you can often receive quicker turnarounds, lower shipping costs, and personalized customer service. Plus, you’ll have the opportunity to work closely with the fabricator to ensure the finished product meets your exact specifications.
Conclusion
Sheet metal fabricators play a crucial role in turning designs into reality. Using a variety of advanced techniques, such as laser cutting, welding, and custom fabrication, they can create intricate parts and products that meet exact specifications. Whether you are in need of a simple design or a complex custom-made product, working with a skilled sheet metal contractor will ensure that your project is executed to perfection.
What's Your Reaction?
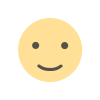
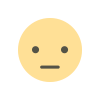
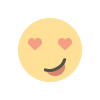
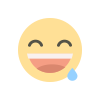
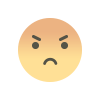
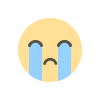
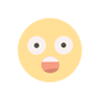